Ça fait pas mal de temps que je n'ai donné de nouvelle de mon Ultimaker, et pourtant, pas mal de chose à dire...
Réception des pièces de remplacement et peinture
Dans un précédent billet, j'expliquais que le colis de mon Ultimaker avait été mal traité durant le transport et que des pièces en bois de l'imprimante était cassées, une erreur s'est également glissée : ils m'avait fourni une pièce ne correspondant pas m'obligeant à usiner une entretoise.
J'ai contacté le support à ce sujet qui à été très réactif car ils m'ont aussitôt expédié un colis avec de toutes nouvelles pièces, réception en moins d'une semaine, merci Ultimaker pour la réactivité.
Quitte à devoir tout démonté et tout remonté, je me suis dit qu'il serait pas mal de la peindre, d'ailleurs, la légende raconte qu'une Ultimaker peinte se sent mieux et du coup, imprime mieux... ;)
J'étais parti pour tout peindre en vert et me suis dit que ce serait plus sympa d'avoir plusieurs couleurs, ce que je n'avais pas prévu, c'est que ça allait me prendre un temps fou, bref, c'est fait mais ce fût long, faute de temps.
Voici le résultat :
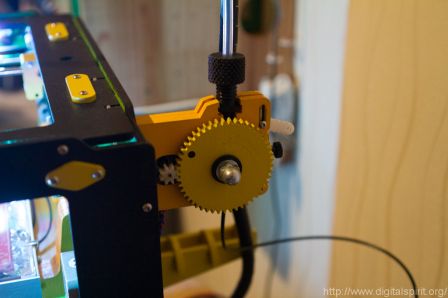
L'extérieur est peint en noir, l'intérieur en vert, toutes les autres pièces fixes en jaune ou orange.
Heated bed
J'ai beau imprimer uniquement du PLA, de légères déformations se forment sous les pièces dû à la rétractation du plastique refroidissant, l'idée est de mettre un lit chauffant (heated bed) permettant de garder la pièce en cours d'impression uniformément chaude.
J'ai voulu faire au plus simple pour le lit chauffant, je l'ai donc commandé, c'est un simple PCB sur lequel est gravé une piste en serpentin faisant office d'élément chauffant, on trouve également 2 diodes têtes bêches servant à indiquer si le lit chauffe ou non.
Les soudures d'origines, de la grande qualité, je fais mieux avec mes pieds :
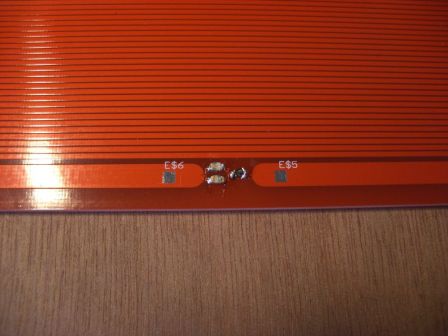
Avant un quelconque montage, j'ai fait quelques tests, ça chauffe parfaitement bien...
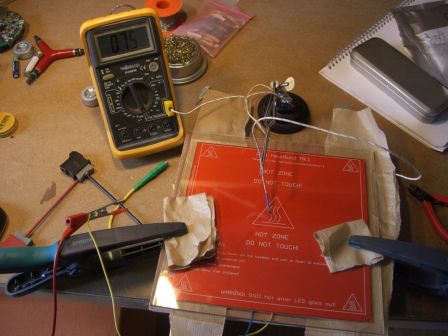
Qui dit lit chauffant dit nouveau support pour l'impression, il est bien sûr hors de question de poser l'élément chauffant sur la plateforme d'origine en acrylique.
Le support sera en bois, en contreplaqué de 10mm d'épaisseur, légèrement surélevé à l'aide d'entretoise, le lit chauffant trouvera sa place, enfin, posé sur ce dernier, on trouvera une plaque de verre à insert sur lequel les impressions se feront.
Les couches successivent : Contre-plaqué, alu, isolant, mylar, lit chauffant.
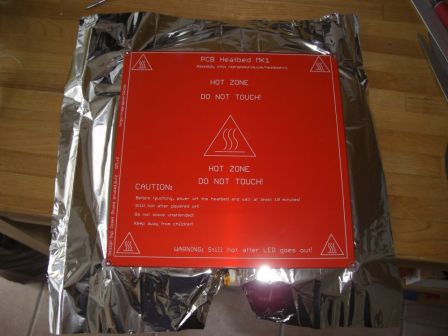
Le nouveau support étant légèrement plus épais que celui par défaut, le réglage du capteur de fin de course supérieur de l'axe Z doit être légèrement modifié, pour cela un simple profilé d'alu à fait l'affaire...
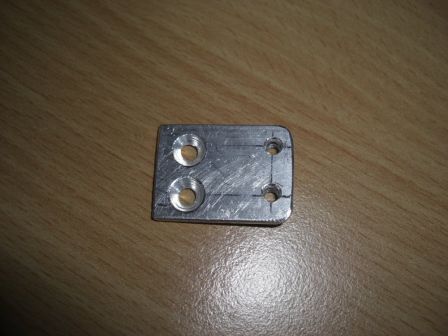
La pièce une fois installée :
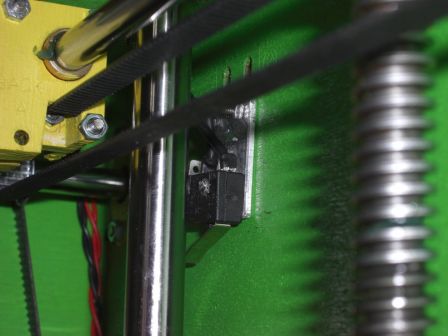
Le réglage du plan se fait à l'aide de 4 vis situées en dessous du support, l'utilisation d'une clef Allen est obligatoire, j'ai prévu de les remplacer par des vis moletées.
L'impression de 4 pièces de remplacement « Z-stage spring-screwblock » (Thing:21480) sans pas de vis à également été nécessaire pour l'adaptation du nouveau support.
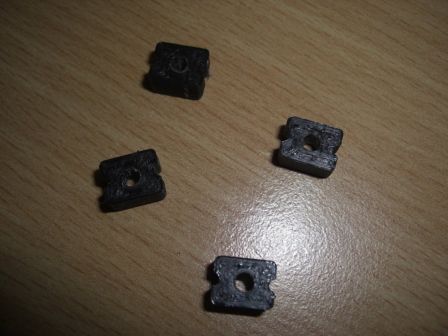
Concernant la partie commande et capteur, j'ai suivi à la lettre les indications d'installation du wiki de Ultimaker, ne possédant pas d'alimentation de 19V suffisamment puissante pour remplacer celle d'origine afin d'alimenter l'imprimante et le lit chauffant, j'ai choisi d'alimenter ce dernier via une source secondaire, ça tombe bien, une alimentation industrielle 12V / 20A toute petite trouvée en brocante pour 3€ ne demandait qu'à servir...
La carte de l'Ultimaker permet d'origine de piloter un lit chauffant, en fait, on vient se brancher sur un des deux Mosfet restants sur 3 (le premier servant pour la tête d'extrustion), j'ai d'ailleurs supprimer le second Mosfet afin de faire de la place pour pouvoir poser un radiateur sur celui pilotant le lit chauffant.
Pour le capteur de température du lit chauffant, il suffit simplement d'ajouter une résistance de 4,7Kohms sur la carte de commande à l'endroit indiqué.
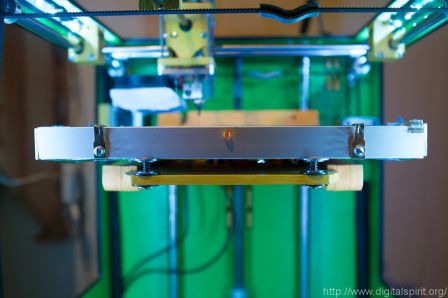
Un peu de lumière
Des réglettes de led multicolores de Ikea trainait dans mon bureau sans réelle utilité, ils en ont finalement trouvé une pour éclairer l'impression.
La surface de travail éclairée :
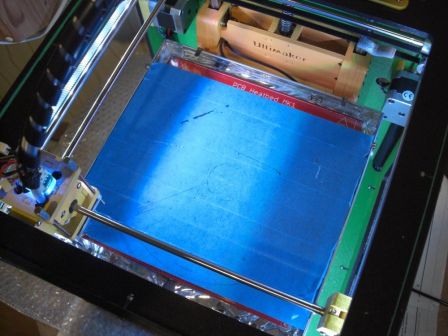
Vue sur les barettes de Leds :
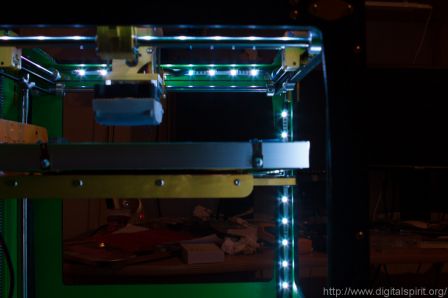
Concernant la connection des leds, je vous déconseille fortement d'utiliser le 12V du ventilateur, ce régulateur chauffe déjà énormément et lui ajouter une charge de 400mA (intensité max des réglettes) pourrait le voir fumer très rapidement, coupant, du coup l'alimentation du ventilateur...Je lui ai d'ailleurs mis un dissipateur car je trouve qu'il chauffait déjà énormément.
Quelques photos en vracs
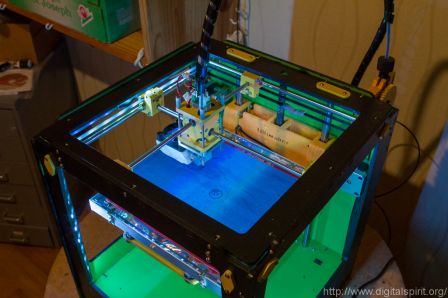
La suite dès que j'ai un peu de temps...